An increasing number of building projects across several markets are using modular construction, the process by which components of a building are prefabricated off-site in a controlled setting and then shipped to the project site and assembled. This approach allows projects to capture the efficiencies gained by integrating the processes and technologies of design, manufacturing, and construction— without having to compromise on aesthetic intent. According to research conducted by McGraw-Hill Construction, when implemented effectively this approach has been shown to result in a higher-quality building, delivered in a shorter time frame, with more predictable costs, and fewer environmental impacts—for example, through reduced material use and waste.
While a range of factors are driving increased use of modular construction, a number of barriers are preventing its wider adoption. And although the planning and design process involved in modular construction is in several ways similar to that of traditional on-site construction, there are some significant differences and a number of considerations that project teams unfamiliar with the modular approach must understand before committing to it. For example, with modular construction many decisions have to be made much earlier in the process. And because a large amount of work is performed off-site, a much higher level of coordination between the various parties involved—on such matters as construction tolerances and scheduling—becomes critical.
Table of Contents
An evolving strategy
Although modular construction has become increasingly popular in recent years, it is not a completely novel approach. In the 19th century, as large portions of the population began to move west—as during the 1849 California Gold Rush—prefabricated houses were transported from New York to California. Prefabricated housing was also popular in the first half of the 20th century, especially during times of high demand, such as the years immediately following World War II. In the late 1950s, modular construction began to be used for a broader range of project types, including schools and healthcare facilities, and in the ’60s and ’70s modular construction began to be used to build large-scale hotel projects.
Now, as technology has advanced and the industry has gained experience with it, the modular construction approach has become increasingly versatile and is used for a wide range of project types, including—in addition to housing, education, healthcare, and hospitality—commercial office, government, and retail.
According to a report published by the Modular Building Institute, an analysis of the market share of permanent modular construction in the North American building industry found that from 2014 to 2016 it expanded across several sectors. In 2016 its market share was largest in the office and administrative (4.86 percent), commercial and retail (3.53 percent), and education (3.50 percent) sectors. And according to Modular Building Institute’s 2018 annual industry statistical report, based on a survey of 252 modular manufacturing firms, in 2017 the permanent modular construction industry drove about $7 billion in construction activity, and the estimated overall market share for permanent modular construction in North America rose to about 3.27 percent, up from 3.18 percent in 2016.
Examples of Modular Construction
A Case Study – Carmel Place
The proposal for Carmel Place, New York City’s first micro-apartment building, won the adAPT NYC Competition, part of the NYC Department of Housing Preservation and Development’s initiative to provide housing for the city’s growing number of small households. The nine-story building includes 55 micro-units (between 250 and 370 square feet, 40 percent of which are reserved for affordable housing), as well as a gym, lounge, roof terrace, and garden, and was the first multi-unit building in Manhattan to be built entirely out of modular components constructed off-site.
The building’s design is meant to serve as a new prototype for a repeatable system of housing that can be easily adapted according to different requirements for height and floor area ratio, and thus be deployable across a range of urban contexts.
The building is made up of 65 individual self-supporting, steel-framed modules. Of these, 55 are apartment units and 10 serve as the building’s core. MEP systems were pre-installed off-site by the modular manufacturer. Appliances and interior finishes were installed after the modules were assembled on-site.
The project’s New York–based design team reported that it was a significant benefit to have the factory located nearby. This allowed for weekly visits during the manufacturing process. Along with giving the team the ability to catch and prevent potentially costly mistakes, the visits allowed them to develop a valuable rapport with the manufacturer that supported the communication and coordination that’s critical for modular construction projects.
A Case Study – Vancouver Affordable Housing
The Vancouver Affordable Housing Agency (VAHA) has developed a strategy of using modular construction to rapidly respond to the urgent need for affordable housing in the city. The city provides the agency use of currently vacant and unused public land for temporary modular housing developments. These projects are guaranteed use of the land for at least three years, after which time they can be disassembled and relocated when the land is needed for a more permanent use. The tenants of these transitional modular housing projects are moved into permanent affordable housing units as they become available. The initial demonstration of this concept, 220 Terminal Avenue, includes 40 units, each with a bathroom and kitchen. The building also includes a shared laundry facility, and shared indoor and outdoor amenity space.
The building is designed to be entirely adaptable so that it can be placed in a range of different sites when it comes time for relocation. If need be, modules can be added, removed, or reconfigured with minimal alterations to the exterior. The building’s above grade, multi-point foundation system is also designed to be easily reusable at different sites. And because this system requires minimum ground disturbance, it is appropriate for temporary use on previously developed sites that may contain environmental contaminants that would require extensive remediation work before construction of more permanent projects. This ability to build without digging up the ground allowed for the safe temporary use of the 220 Terminal Avenue site.
VAHA reported that the development approvals process was overly complex and time-consuming on this initial project, eroding some of the benefit provided by modular construction and acting as a barrier to the goal of expediting the creation of affordable housing. To address the issue, the agency has recommended that city staff be authorized to work with project teams on variances for relevant zoning and development regulations.
Factors driving use
Participants in a 2017 survey of property owners conducted by FMI in partnership with Construction Users Roundtable and the Construction Industry Institute stated that a shortage of skilled labor available for on-site work and increased pressure on project costs and schedules are primary reasons for the increasing popularity of off-site construction. In addition, improved technology allowing for greater applicability and customization, heightened concerns regarding safety and risk, and an increasing demand for higher quality were also stated as factors contributing to the growing interest in off-site approaches.
Increasingly urgent demand in the housing, hospitality, and healthcare markets is also driving more projects to use modular construction. As many cities across the country are experiencing severe housing shortages, modular construction—with its potential to significantly increase the speed of delivery while also providing opportunities for cost savings—is seen as a strategy that’s particularly well-suited to address the issue.
For example, to address the severe lack of affordable housing in London, the city announced in 2017 that it would dedicate $32 million to construct a minimum of 1,059 affordably priced modular apartments by the year 2021. (In a study of the UK construction industry, KPMG found that by using off-site construction “financial net savings of 7% were possible as a consequence of the shortened construction period.”) In the spring of 2018, the New York City Department of Housing Preservation and Development released a request for proposals for an affordable housing project in Brooklyn that requires modular construction methods. And according to Modular Building Institute, urban areas such as San Francisco, Seattle, and Vancouver are now considering modular construction as a means to address homelessness as well as to provide affordable housing for lower-and middle-income families.
What are the types of modular construction?
In general, modular building elements prefabricated off-site are either constructed as non-volumetric components or as volumetric units.
Volumetric modular construction involves the off-site prefabrication of individual three-dimensional units of enclosed space that are then connected on-site to form a single building. For example, volumetric modular construction is often used for multiunit residential projects like hotels, dormitories, and apartment buildings. Each unit, depending on its size, may be made up of one or more modules. Other examples of volumetric elements include patient rooms, bathroom pods, and sections of elevator or stair cores.
Non-volumetric modular construction involves the off-site prefabrication of building elements (commonly referred to as sub-assemblies) that are then connected once on-site. Common examples of non-volumetric modular building elements include:
- Structural elements such as frames, beams and columns
- Sections of building façade and cladding
- Wall panels and interior partitions
- Floor cassettes and planks
- Roof trusses
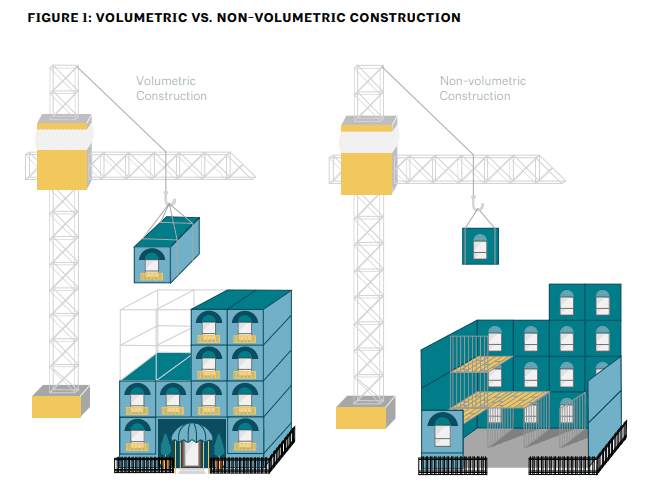
Modular projects may be composed of a combination of volumetric and non-volumetric components, and projects may utilize a combination of off-site and on-site construction, depending on the specific requirements of the design, program, and/or site. For example, components needed to form large openings or spans, which may be difficult to manufacture in an off-site facility, are commonly built on-site.
Although non-volumetric elements may be transported more compactly than volumetric units, potentially reducing transport costs, they require additional assembly and sealing work on-site, the cost of which may offset any transport savings gained. However, it should be noted that the total time and labor cost for non-volumetric modular construction is generally still significantly lower than traditional on-site construction.
While this guide will focus primarily on volumetric modular construction, many of the principles will also apply to other off-site fabrication technologies, including non-volumetric panelized construction. Although small-scale modular buildings are often used in non-permanent installations for such purposes as temporary offices, classrooms, and emergency relief housing, this guide will focus on permanent modular construction, which can be used at all scales, from single-family homes up to highrise buildings. It should be noted that while a majority of modular projects are four stories or less, in recent years an increasing number have exceeded 10 stories, and modular construction can be used to build structures up to any height, unless otherwise restricted by the local code.
Varieties of volumetric modular construction
Volumetric modular components may be manufactured as structural or non-structural components. For example, a modular building may be manufactured as a set of structural units that together form the structure of the building once assembled on-site, or as non-structural units— such as bathroom pods—that will be set within a superstructure, the components of which may be constructed either off-site or on-site. In most cases, the modular manufacturer will take on structural engineering responsibilities. The structural requirements of modular projects can be relatively intricate, and it is generally one of the biggest differences compared to traditional construction techniques. Architects should note that in cases where the modular manufacturer assumes responsibility for the structural design, it would involve a significant shift in risk and may require a change in the architect’s scope of services.
Modular building components may be manufactured from a range of different materials—including steel, concrete, and wood—and can meet the requirements for Type-I, -II, -III, and -V construction. But the modular approach can be most readily applied in Type-II and Type-V construction, for which it is most commonly used.
Although wood-frame has been the most common type of modular construction (70 percent in 2017, according to the Modular Building Institute), over the past five years there has been a shift towards more steel-frame modular construction. This trend may in part be explained by the fact that modular construction is being used for taller buildings, where the preference is for steel.
A project may combine a variety of materials and assembly types; however, it should be noted that in order to maximize efficiencies in the manufacturing process, many modular manufacturers focus on a specific type of construction and not all will be equipped to offer a full range of material options.
Generally speaking, when implementing the volumetric modular approach, up to 95 percent of the building will be fabricated off-site, according to the Off-Site Construction Council of the National Institute of Building Sciences. The level of finish that is applied off-site generally ranges from 50–90 percent and will depend on a number of factors, including the building type, site constraints, project location, and local on-site labor rates. The optimal degree to which the components of a modular building will be prefabricated—and the level to which the components will be finished—will vary from project to project, but the general aim of modular construction is to minimize the amount of work that occurs on the building site. The more work that can be completed off-site in the controlled environment of a manufacturing facility, the greater the efficiency gained and the lower the risk of such factors as weatherrelated damage to materials and mistakes due to miscoordination between trades. Additionally, the less work taking place on-site, the less disruption and disturbance to the surrounding community.
Modular off-site construction thus involves significant integration of the design, fabrication, and construction phases of a building project. A key reference for this approach is Design for Manufacture and Assembly (DfMA), a concept based on a holistic understanding of the production process, emphasizing design that facilitates the fabrication, shipment, and installation of a product. Applying this idea to modular buildings, project teams not only design the building’s various elements, they also plan the process of how those elements will be manufactured, moved to the site, and assembled.
The Manufacturing process
Because the fabrication of modules should be considered as part of the design of modular projects, it’s important for designers to have at least a general idea of how the modular manufacturing process works. For example, designers should understand the central role of digital technologies in the fabrication of modular components, including building information management (BIM) tools, computer aided design (CAD) tools, computer aided manufacturing (CAM) tools, and computer numerical controlled (CNC) machinery. Designers should also understand how these tools can support mass customization, the method by which modular manufacturers produce custom designs at a cost-effective industrial scale using a range of standardized components.
Unlike traditional on-site construction, in which the building is generally completed from the outside in, prefabricated volumetric building modules are typically constructed from the inside out. In such cases, the box frame of the module is first completed, then interior finish is added, MEP components and insulation are installed, and, finally, exterior sheathing and cladding is applied.
However, although this general sequence is common, it is not the only way building modules are manufactured. Different manufacturers may have different processes, and it is important for project teams to understand the specific methodology of the manufacturer they select to work with. For example, while some manufacturers may employ a linear production process in which the tasks of each trade are performed sequentially, others use a static production process in which modules are worked on by the various trades simultaneously.

What are the advantages of modular construction?
A primary reason why more projects are using modular construction is that there is increasing recognition of the benefits the approach offers. As mentioned earlier, because modular construction involves conducting the bulk of the construction process off-site in a controlled setting, it can contribute to improved quality, less waste, increased control of cost, and reduced risk.
Quality
Applying the efficiencies and controls of highly evolved manufacturing processes to building construction produces several significant benefits. The monitored manufacturing setting, the use of precise fabrication tools such as CAD/CAM, and the ability to automate processes allow for a high level of quality control and consistency. This quality control is especially beneficial when it comes to the installation of sensitive high-tech components such as fire and security systems or sensor-based environmental controls. The increased precision in fabrication of exterior wall components also results in a much tighter building envelope with fewer air leaks.
Depending on the complexity of the project’s program and building form, mass production manufacturing processes can be used to achieve additional economies of scale. Additionally, utilizing mass production processes does not necessarily translate into a loss of design flexibility. Project teams can work with fabricators to pursue a mass customization approach that captures the benefits of mass production economies of scale while allowing variability to suit a wide range of client requirements and design intents.
The production and storage of building components in an enclosed facility also results in reduced exposure to the weather, which can cause moisture-related damage during construction and, in turn, decrease the durability of the components and increase the potential for mold growth that’s harmful to occupant health.
Productivity
Labor productivity is also increased when using an off-site approach. A crew working in a plant is less affected by adverse weather. Additionally, a crew equipped with precise tools and machinery, working in a space designed to provide ideal conditions for manufacture, is able to achieve higher levels of quality in a more efficient manner. Off-site construction also means a more consistent crew and a more controlled workflow that will be less prone to disruption.
In addition, as a modular construction approach requires a high level of coordination and collaboration among project team members, it promotes a more integrated process that can in turn lead to increased productivity during the design and planning stages of the project.
Safety
An off-site construction approach is also generally safer for workers. Workers work in a controlled setting and are not exposed to the hazards of extreme weather and other construction site dangers such as those related to noise and air quality. According to the U.S. Labor Department Bureau of Labor Statistics, rates for fatal injuries are, overall, substantially lower in manufacturing than in traditional onsite construction.
On top of increased safety, moving construction work to off-site manufacturing facilities could improve the overall culture of construction work, for example, by providing greater job security and more flexible shifts for workers.
Schedule
Prefabricating the bulk of a building in an off-site facility means that the construction process is much less vulnerable to delays due to poor weather conditions. This facilitates a more predictable schedule. Off-site construction also allows for work that would usually need to be sequenced to be performed simultaneously. Compared to the linear process that generally characterizes traditional on-site construction, with trades working sequentially, off-site construction allows trades to work concurrently.
In addition, if a project is coordinated so that site work and pre-construction engineering is conducted at the same time that building components are fabricated off-site, the construction schedule can be shortened by 30 percent to 50 percent, according to the Modular Building Institute, resulting in dramatic schedule savings. If true, this is a significant benefit over conventional on-site construction that requires the completion of the foundation before work on the building can begin. The more work that can be completed off-site, the greater the savings due to the increased amount of time saved on-site.
Delays related to supply chain issues may also be reduced by using off-site construction, as modular manufacturers may often have more firmly established connections with a larger network of qualified material suppliers as well as a greater ability to store bulk materials compared to traditional on-site operations.
Further savings can be gained through close coordination between on-site and off-site operations. Ideally, building components should be fabricated, transported, and delivered to the site “just-in-time,” according to when the site infrastructure required for their installation has been completed, avoiding any additional costs for storage at either the plant or the construction site.
It should be noted that reductions in schedule may depend on the complexity of the project or the level of customization involved. Although a benefit of modular construction is that it allows for greater technical complexity in design, complex projects that require many unique components will require more fabrication time—as well as assembly time—than projects using more standardized elements.

Cost and value
Although modular construction can be more cost efficient than on-site construction, this does not automatically mean it will result in a reduction in overall project cost. However, the costs are often more predictable than with traditional construction methods. If affordability and controlled cost is of primary concern on a project, modular construction can be used to achieve it, but it will require greater intention in design and thorough planning.
The cost for any particular modular project, as with any conventional project, will vary according to a range of factors. Project teams should consult with a modular manufacturer when determining the various specific factors that will impact the cost of the project, and to what extent. For example, in some cases modules may need to be overbuilt in order to meet transportation and set requirements. In other cases, depending on the modular manufacturer, more complex designs may increase the fabrication cost if more expensive materials are needed, more production time is required, or the facility must be retooled in order to construct the necessary components.
As well, the modular manufacturer’s expertise is useful in determining the most cost-effective way to handle transportation of modules. As with fabrication costs, the transportation cost for any particular modular project will depend on a number of variables, including, for example, the trucking distance between the fabrication facility and the job site, and the number of trips required.
In most cases, all modules will be over-dimensional loads, and a special permit will be required to transport them on public roads. Depending on the project and location, it may be determined that it’s more cost-effective to make the modules as large as possible within regulations and pay for a police escort or special routing in order to reduce the total amount of modules and minimize the number of deliveries. This strategy would also limit the number of crane lifts required, which could offset the higher cost of larger cranes needed to lift larger components.
Ultimately, when analyzing the cost of modular construction compared to conventional construction for a specific project, it’s important that all hard and soft costs be taken into account. Overall, modular construction should be understood as a lifecycle investment. Regardless of the upfront costs, if implemented correctly it will prove to be a more cost-efficient way to create value in the long term, and the decision to use modular construction should ideally be made based not on an upfront cost comparison but rather on a clear understanding of the particular benefits the approach offers and the extent to which these align with what the project owner values in each particular circumstance.
Sustainability
Modular construction can also contribute significantly to the environmental sustainability of a project. For example, the off-site production of building components allows for optimal control of material use, resulting in both reduced material input and waste compared to traditional on-site construction. Additionally, a significant amount of surplus material and fall-off can be captured and recycled back into the inventory for use on other projects. Generally speaking, the greater the portion of a project that is fabricated off-site, the greater the benefits gained by optimizing the input of materials and reducing material waste.
Project teams can also work with fabricators to select materials and products that will further minimize the impact of material extraction, processing, and transport. For example, specifying regionally sourced and responsibly produced materials (FSC-certified wood, for example), can reduce the project’s embodied impacts associated with transportation of materials and depletion of natural resources, including loss of forests.
Because building components for several projects can be fabricated simultaneously at a single plant and shipped nearly complete to building sites, the amount of worker travel and small material deliveries are drastically lowered with modular construction, also resulting in significantly reduced emissions from transportation.
The operational energy of modular projects can also be reduced through the increased and more reliable thermal performance that can be gained by the precision, quality control, and consistency inherent in the off-site production of building envelope components under controlled manufacturing conditions. Additionally, because modular construction approaches generally result in fewer seams and joints to be completed on-site, it naturally lends itself to achieving very high levels of air tightness, such as those required by the Passive House Institute performance standard.
Modular construction generally requires less space around the building site for workers, truck traffic, and material storage, resulting in a smaller construction footprint and reduced site disturbance.
And because the on-site portion of the modular construction process is shorter than traditional construction methods—involving fewer workers and less traffic.
Modular construction for long life, loose fit
With modular design there is also an opportunity to include a kind of “plug and play” flexibility that could allow for modular buildings to be easily adapted or modified for different purposes over time. As well, modular components could be designed for disassembly and reuse so that a modular building could be deconstructed into parts to be reconstructed elsewhere or be redistributed for incorporation into multiple other projects. But even if modules are not reused, modular buildings designed for disassembly would be easier to decommission and remove in a more controlled way that should be cleaner and less environmentally impactful compared to buildings constructed and demolished using traditional methods.
Furthermore, as construction practice evolves, and more attention is paid to reuse and recycling, the industry may eventually be equipped to reclaim the structural elements from modules for reuse. Large components such as beams, columns, slabs, and walls could be given unique identifiers linking them to informational databases, making it possible for these components to be systematically stored and reallocated for use in new projects according to their design capacities. Project teams can further increase the recyclability of modules by designing smaller assemblies and elements for ease of disassembly and separation into material categories.
What are the disadvantages of modular construction?
Despite the range of benefits that modular construction offers and the several factors that are supporting its increased use, certain barriers are slowing the rate at which the approach is adopted. Participants in the aforementioned survey of owners stated that only 33 percent of capital projects currently use modularization.
For example, there is still a limited supply chain. Currently, many modular manufacturers focus on specific market segments and on low- to mid-rise buildings and are not readily able to produce a wide range of project types and sizes.
There may also be some confusion about how the building code is applied on modular projects. Projects using off-site modular construction must comply with the same building codes that pertain to conventional on-site construction; there are no special provisions pertaining to the use of modular construction. However, as the applications and approvals process for modular construction differs from that for conventional construction, it can act as a barrier for project teams unfamiliar with it. Although many states now have governmental programs to regulate modular construction and provide project teams with requirements on the alternative applications and approvals process for modular construction (discussed in further detail below), some states do not.
Mis-perceptions
A general lack of experience may also keep owners and project teams from feeling comfortable with modular construction. But this is likely to change over time as more in the industry gain familiarity with the approach.
Those unfamiliar with modular construction may mistakenly believe that it is an all-or-nothing strategy, but most projects could use any number of modular components, employing a combination of modular and traditional construction to create a hybrid approach that still provides many of the benefits of modular construction. For example, a project may benefit from fabricating only the more standardized repetitive elements off-site while simultaneously constructing the architecturally unique components such as entryways elevators and stairwells on-site.
Some architects may also believe that modular construction limits their design options or restricts their control, but in fact it can accommodate a wide range of forms and styles through mass customization methods, offering a lot of design freedom. This is evidenced by the wide variety of projects—including the case studies found throughout this document and projects available through the Additional Resources—that have recently been built using modular methods.
Additionally, the opportunities provided by mass customization approaches may ultimately increase the architect’s ability to tailor the design of manufactured components. For example, parametric design tools, when integrated with advanced BIM modeling and the precision of computer-aided fabrication technologies, could potentially provide architects vastly expanded control of the formal qualities of modular building components. Additionally, rapid prototyping techniques can foster more sophisticated and informed iteration by providing architects an increased opportunity to evaluate full-scale mock-ups of custom-fabricated components.
Differences compared to traditional construction
The different funding models commonly involved in modular construction may also make some owners reluctant to try it. For example, modular projects can require higher upfront costs for technical approval compared to traditional construction projects. Ensuring compliance with building codes may increase the scope of engineering work and result in higher upfront costs compared to traditional projects.
Modular construction may also involve a different cash conversion cycle because construction time can be substantially reduced. Owners shifting to modular construction may need to revise their financing arrangements. It should be noted, however, that by shortening construction time there is opportunity to reduce overall development financing with modular construction—as revealed by the KPMG Smart Construction report. The shorter the construction period, the fewer the developer’s carrying costs and the sooner the project will return a profit.
There may also be special challenges to address if a project is publicly funded—depending on the state in which it is located and local requirements relating to procurement—as modular construction differs significantly from traditional construction in this regard. For example, a modular project that will be constructed almost entirely off-site will have a schedule that may not fit with a typical AIA schedule of values on which monthly progress payments would be based. This creates a challenge regarding payment certifications that some publicly funded projects may not permit.
There is also some resistance to modular approaches in the construction industry from some trade unions. Because modular construction involves an increasing level of standardization and industrialization, some argue that it reduces the need for traditional trade labor. However, advocates of modular construction argue that modular construction—which utilizes rapidly advancing technologies, tools, and techniques—will lead instead to new and more appealing professional opportunities in the construction industry, particularly for younger workers. Others simply point out that off-site construction is necessary to address the general trend of reduced availability of skilled labor.
Some argue that a cultural shift in the industry as a whole is needed before the full benefits of modular construction are realized on a broad scale. One way to encourage such a cultural shift in practice might be to start including alternative approaches like modular off-site methods in the curriculum of architecture and construction education programs. (For information on how institutions of higher education are teaching about off-site construction methods, see this survey conducted by the https://www.nibs.org/resource/resmgr/images/nibs_logo_wt.png Off-Site Construction Council, Associated Schools of Construction, and Association of Collegiate Schools of Architecture.)
Other factors to consider
Finally, some aspects of modular construction may make it a less advantageous choice for certain projects. When considering modular construction as a potential approach, project teams should consider the following:
- Modular manufacturers may not be able to cost-effectively produce highly complex forms.
- Modular construction may require some additional time for approvals and inspections in places where the local jurisdiction is less familiar with off-site fabrication methods. (However, this issue would be bypassed in the many states that now have dedicated programs responsible for modular off-site construction.)
- In general, modular construction can result in a bulkier structure, as each module has its own independent walls, floor, and ceiling. This means deeper floors and thicker walls compared to traditional construction. While this may be beneficial in terms of acoustics, energy efficiency, and thermal comfort, it could also negatively impact interior living spaces in taller structures—by reducing the usable area and volume of interior space—if not properly considered during design. A building with very expansive clear spans and considerably high open ceilings—for example a “big box” store—is not conducive to modular construction.
Additionally, there are some circumstances that are not ideal for modular construction and in which the benefits of the approach are unlikely to be fully realized. For example, building sites that are easily accessible and located on affordable land in climates that allow for year-round construction work may be less likely to benefit from off-site fabrication’s otherwise faster delivery.
Likewise, if the project is in a location with excellent access to affordable materials and labor, the potential cost savings provided by an off-site approach may be reduced compared to locations where the materials and labor are more expensive. However, environmental benefits that can be achieved by optimizing the amounts of materials used, and reusing or recycling scrap directly in the prefabrication process, would still accumulate. Similarly, the length of disturbance to neighboring properties, and the community at large, would be shorter even in these circumstances.
Modular Construction in Practice
When determining whether modular off-site construction is appropriate for a certain project, stakeholders should first of all understand the process well enough to be able to evaluate to what extent it will aid the project in meeting goals pertaining to cost, time, labor, site, and program. Certain aspects of a project make modular construction an ideal approach. For example:
- Projects where schedule reduction or time to market is a primary motivator for the owner
- Projects with repetitive elements such as identical classroom units, dormitory units, office spaces, or labs
- Projects with relatively dense framing and no excessive spans
- Projects located on remote or less accessible sites where on-site construction would be difficult—as in dense urban areas—or in locations with constricted build seasons or where materials, labor, and/or land is expensive
- Projects located in areas where labor is not readily available
It should be noted that, in the absence of these aspects, modular construction can still be a viable and competitive process, but the full advantages of the modular process may not be realized.
Further to these considerations, it is important to recognize that (as discussed in further detail below) the modular construction approach may require the design team to take on new and different responsibilities beyond those traditionally assumed by the architect. For example, a modular building design should take into account the manufacturing process, transportation issues, and sequencing— some of which are more traditionally considered construction means and methods. On most modular projects the architect will rely on the manufacturer to provide information and in some cases perform structural design work, which usually requires more nuance than on traditional construction projects.
This requires that services, responsibilities, and liabilities be clearly and adequately delineated. Due to the fact that the modular construction approach may require changes to some traditional design services, architects should consult their insurance carrier and local attorney before undertaking a modular project so they can understand the issues involved and make a fully informed decision.
Commit early
Effective implementation of modular construction requires a commitment to early planning and decision-making. For this reason it is crucial to commit to the approach from the outset of the project. Deciding to use a modular approach after the design development phase may not yield the desired advantages of modular construction.
Modularization involves more than taking a traditionally designed building and cutting it up into components. Ideally, a modular-based design philosophy should be adopted from the start, ensuring that various considerations—including those related to geometry and material strategies, transportation logistics, and issues related to shared scope and coordination—are fully integrated into the process. In general, designing with modular construction in mind from the very outset is one of the best ways to maximize the benefits and efficiencies the approach offers.
Especially for project teams new to modular construction, it can be beneficial to consult with a modular manufacturer as soon as a schematic concept is developed, if not sooner. In some situations, the party responsible for the off-site fabrication of modules—either the general contractor or a modular manufacturer under contract with the general contractor—may share some of the responsibility for design work to ensure the project will meet best practice requirements for modular construction. In particular, the modular fabricator may take ownership of the structural design. Depending on how design responsibilities are delineated and the fabricator’s scope on a particular project, this design assist process may require a significant adjustment for project teams that are new to it.
A major difference when designing for modular construction is that it requires that more decisions be made at an early stage in the process. For example, on traditional construction projects it is typical for design work to overlap some with the construction process. The design of interior spaces, for example, often continues while the building’s structure is being constructed. But on modular projects this is not feasible. Space planning, details, and service integration are all typically completed earlier on modular projects because incorporating design changes to modules once fabrication has begun can be very expensive. This difference should be understood and accepted before committing to a modular approach.
Predesign
Legality, financing, and insurance
During the early pre-design phase, the project team should clearly establish which party is responsible for the modular components—and for the associated financial and insurance liability—at each point in the process, particularly during the transportation and delivery of modules to the job site. When implementing modular construction, project teams will have to consider some unique issues related to financing and liability. For example, modular projects do not easily fit into traditional lender calculations because modules delivered to the site ready to be installed are categorized as materials. Most of the vertical construction takes place off-site, which shifts the typical construction project balance based on the expected percentage of labor versus material.
Modular construction also involves particular risks that need to be considered and insured against. For example, there is risk related to the transportation of modules and the increased use of cranes for assembly on-site. In general, the probability of significant damage to modules during transport is relatively low, and repairs—which would likely be performed on-site—would be covered by the carrier’s insurance. In most cases, as delivery is usually included as part of the manufacturer’s contract, it would be their responsibility to coordinate with the carrier to confirm that the carrier’s insurance will adequately cover transportation risks.
Unlike traditional site-built projects, where the labor cost typically makes up about 60 percent of the total project cost, on modular projects a large amount of the labor that’s usually performed on-site occurs off-site. This will influence the specific insurance policies that need to be put in place. For example, wrap-up insurance policies such as an owner controlled insurance program (OCIP) and contractor controlled insurance program (CCIP) are not feasible.
In addition, if completed modules will have to be stored at a location off-site due to schedule delays, the project will need to obtain a provision amending the coverage of builder’s risk insurance because property stored off-site would not typically be covered.
Regarding worker’s compensation, the following classifications should be used for modular construction operations, according to the National Council on Compensation Insurance:
- Code 2797 for all modular manufacturing operations, including fabrication shop work and transportation of modular components by the fabricator
- Code 2799 for all modular setup, assembly, and installation operations taking place at the project job site, including all delivery and on-site placement work performed by specialty contractors
Delivery model
Generally speaking, the traditional design/bid/build model is not particularly well-suited to modular construction methods. With this model it’s generally the case that the owner and project team develop a design in isolation from contractors until the bid process, by which time the design has advanced to the point where the team may be unwilling or unable to make changes to optimize for modular construction.
Furthermore, whether the evaluation of bids is based on lowest cost or on other values (sustainability, schedule, experience, etc.), the design/bid/build model is defined by a sequential schedule, with each party acting in relative isolation before handing the design off to the next. This linear process is disadvantageous because it often results in poor communication between the design and construction team, ultimately lengthening the project schedule.
The highly collaborative and iterative nature of design/build and Integrated Project Delivery (IPD) models make them much more ideal for modular construction. In the design/build model the design phase and construction phase overlap, with the architect and contractor coordinating on the design as it develops. For modular projects, the modular manufacturer would also be included in the design/build team to provide direct feedback regarding fabrication during the design process. For example, at the outset the manufacturer should explain to the team any constraints imposed by the module production and transportation processes. This model also allows for real costing to be established earlier on in the process so that adjustments can be made during design to ensure that the project meets budget.
Similarly, with the IPD model the modular manufacturer, along with other key consultants, will be involved from the outset of the process, allowing them to provide guidance throughout and coordinate more effectively. The IPD model is in many ways ideal for modular construction, which relies on a high level of integration not only in terms of collaboration between teams during design, but also in terms of how the building is conceived and developed as a more intentionally integrated system of prefabricated products and components to achieve the highest possible performance.
Regardless of which variety of delivery method is used, the project team should ensure that it will allow for the early involvement of all necessary consultants and enable the level of information flow required to successively implement modular construction. At a minimum, it is ideal to involve both a modular manufacturer and a construction manager early, as these are the parties that will be responsible for the two primary components of modular construction: off-site operations and on-site operations, respectively. Early and ongoing coordination between these processes will be critical to the successful implementation of modular construction. (It’s also possible to have situations in which a single general contractor is responsible for performing both the off-site fabrication and the on-site construction.)
Compliance
Project teams should coordinate with the construction manager early in the process to determine what the local permitting requirements will be. Modular buildings will need to meet all applicable codes in the city and state where it will be located, regardless of where it was manufactured; project teams should ensure these code requirements are communicated to all parties, included in specifications, and integrated into the project planning process from the outset of design.
It should be noted that although the code requirements for modular projects are the same as those for conventional projects (based, in most jurisdictions, on the International Building Code), and there are no special provisions regarding modular construction methods, the ways in which the codes are applied and inspected differs for modular projects.
While many states have a specific modular building program with jurisdiction over inspection of three dimensional modules prefabricated off-site—and responsibility for approvals of manufacturers, quality assurance and control measures, and plans—some states do not. In such cases, the local authority having jurisdiction is responsible for enforcing code compliance on modular projects.
In states with a dedicated modular construction program, projects will submit drawings for modular components to the statewide program for review and approval. Depending on the state where the project is located, code compliance inspections may be required to be conducted at the manufacturing facility, on-site, or both. Generally, a state-licensed third-party design agency will conduct the off-site inspection, if required. Each module will be issued a label signifying compliance with the applicable building codes at the final site of the building.
Site work and any other fabrication work that does not fall into the modular construction scope will be reviewed and inspected by local agencies. In jurisdictions where modular construction is not yet common, projects teams should seek early engagement with local authorities to determine, as soon as possible, what will be required for compliance.
(To check the appropriate administrative programs and codes for modular construction in a particular jurisdiction, see the Modular Building Institute’s Building Codes search tool.)
Design
Engage a modular manufacturer
Generally, once a modular project is ready to proceed beyond schematic design, the modular manufacturer should be brought on to provide consultation and, potentially, design-assist services. The earlier this happens, the better—especially for project teams new to modular construction. Having the modular manufacturer involved early allows the project team to benefit from the manufacturer’s expertise and knowledge of available products and techniques.
In most cases, because the structural design is one of the most critical elements of modular construction, the modular manufacturer will take on the structural engineering package or, at a minimum, provide structural design-assist services. As modular manufacturers are generally more experienced with the complexities of modular construction, they are better able to check that related efficiencies are gained, and associated risks are addressed during the design phase. Architects should understand that this involves a fundamental shift in traditional design responsibilities.
In addition, consulting the modular manufacturer early enough may also help the project team do the following:
- Maximize flexibility in design options.
- Ensure that design specifications do not require materials or products that may extend the schedule due to long lead times.
- Promote value engineering by making suggestions that could help lower costs or improve schedules.
- Control and reduce transportation costs, where possible, by comparing transport costs per module to installation costs per module at site.
- Control and reduce construction costs, where possible, by optimizing the module key plan.
- Ensure constructibility of the design by advising if any design criteria are impossible due, for example, to transport restrictions and assist with developing alternative solutions.
- Design for efficiency and reduced waste.
- Minimize risk throughout the process.
The architect should be careful to clearly establish the specific scope of the modular manufacturer’s responsibility related to these services. It may become problematic if the modular manufacturer’s role in the design process is vague, creating confusion around who is responsible for what. What information for which the design team will be able to rely on the modular manufacturer should be established from the outset of the design process.
Often the manufacturer will primarily act as a consultant, answering questions and providing feedback on a design. However, in some cases the manufacturer may take on substantial or full design responsibility for an element, such as the structural system, as discussed above. In such cases, the manufacturer should take on full legal liability for that system.
When selecting a modular manufacturer, the project team should research the industry—for example, by requesting referrals and reviewing case studies of similar projects—and issue pre-qualification
questionnaires to create a shortlist of potential companies. The following factors should also be included as criteria in decision-making:
- Level of experience with specific project type and level of design complexity
- Production capacity relative to project scale and schedule
- Extent of established network of resources
- Proximity of plant location(s) to project site (Most manufacturers will ship to locations within about a 350- to 500-mile radius.)
The modular manufacturer selected must be approved in the state where the project will be located. And depending on the project location and scope of its responsibilities, the modular manufacturer may also need to be licensed as a general contractor, plumber, electrician, or structural engineer.
Generally, it is better for the modular manufacturer to act as a subcontractor that is building to specification rather than as a supplier that is designing a product. This avoids issues related to product liability and the Uniform Commercial Code, which includes various rules pertaining to the sale of goods that are usually not appropriate for building construction.
When it comes to defining the modular manufacturer’s scope, three common approaches may be used when implementing a modular construction approach:
- The modular manufacturer acts as a subcontractor and hands off the completed modules to the general contractor responsible for completing the project on-site.
- The modular manufacturer acts as a subcontractor that also performs the installation of the completed modules but is responsible for nothing else.
- The modular manufacturer acts as the general contractor, responsible for all aspects of the projects, off-site and on-site.
Coordination
The success of a modular construction approach is contingent on how well information is shared between the various parties involved, especially the design team, the modular manufacturer, and the on-site construction management team.
Before design commences it is critical to clearly define the responsibilities and scope of work of each project team member. Project teams should produce a detailed document recording this information to ensure that all costs are captured during the pricing stage and to reduce the risk of potential gaps or overlaps in scope. With modular construction it is especially important to demarcate work that will occur off-site from that which will be performed on-site as well as to specify who “owns” each module when.
Additionally, construction tolerances and interface details of how components fabricated off-site will connect to elements built on-site are critical pieces of information that must be clearly communicated to all project team members. Sequencing should also be well-planned and clearly communicated as early as possible. When it comes to maximizing the benefits of the modular construction, timing is everything. The schedule efficiencies offered by the approach can be reduced or lost if the overall process,—from the preliminary design phase all the way through—is not well organized. A detailed timeline with milestones should be shared with all team members and regularly reviewed.
It should be understood that in cases where the design team will take on the task of managing the increased coordination and sequencing involved in the modular design and construction process, it would amount to an expansion of the responsibilities traditionally required of the architect.

BIM
Building information management (BIM) tools like Revit can contribute significantly to a wellcoordinated design, manufacture, and assembly process. For example, BIM can be used to plan sequencing to ensure that construction tolerances are maintained, and the clash detection features of BIM tools can help avoid conflicts at mate lines.
BIM may also provide greater flexibility in design by allowing for robust, data-supported virtual prototyping. By consolidating project information, BIM could also support efficiency by minimizing the need to exchange data between different design, manufacturing, and construction management tools, and by allowing for visualizations of the on-site assembly process. But it is essential that the project team establish thorough BIM standards for all parties to adhere to in order to avoid errors that could compromise the accelerated schedule.
Integrated process
As discussed earlier, the principles of Design for Manufacture and Assembly—which emphasize a holistic understanding—can be used to inform the way a modular-based design process works. Basically, when designing a modular building, architects should address not just the design of a structure and its constitutive components; they should also be intentional about the process by which these are fabricated, transported, and connected. The design of individual modules may be affected by the requirements of the manufacturing and assembly processes while, at the same time, the parameters of the design will dictate the ideal execution of those processes. For example, designers must address how mechanisms for connection to other modules will be integrated into each module.
When designing for modular construction, the project team should shift their perspective to thinking of the building as a system of connected components. This view can help open up a larger field of possibilities for how modularization might be implemented, leading to a more iterative and less linear design process. The concept of modularity should ideally be embedded in and inform all phases of a project, not just the construction phase.
Initial design considerations
The basic aspects of modular construction should be used to guide the early design process, as some may constrain the design’s development.
The geometric design of the constituent modular components (and, ultimately, of the building as a whole) will also be affected by transportation-related constraints on the size and shape of modules. Further, the manner in which the building will be divided into modules will affect the design of interior layouts and floor plans.
Parametric design tools can provide for a wider range of options in modular construction. The design team may experiment with these tools to create variations of the standard module to be used on a project while remaining within the parameters defined by what the manufacturing process can costeffectively achieve.
Teams may also consider collaborating with the modular manufacturer to build prototypes—or mockups of components or entire modules—as a way to evaluate the constructability and performance of different design options. In addition, any specialized details and components should be reviewed with the modular manufacturer as early as possible to determine if they can be practically adopted into the modular design and, if not, to discuss alternative means of achieving the design intent.
Connections
In order to ensure ease of assembly and potential for disassembly, the design team will need to carefully consider not only how modules will connect to each other, but also how the modules connect to site-built components, including the building foundation, structural elements, and, on larger projects, elevator and stair cores.
Detailing should be developed in close collaboration with both the modular manufacturer and the construction manager. In particular, the manufacturer should play a leading role in the development of interface details for module-to-module connections and module-to-foundation connections.
Design teams should rely on the manufacturer’s input in order to develop details that optimize the manufacturing process and simplify installation. This may involve—especially on larger projects— the inclusion of placement aids to help the on-site team identify where within the structure each component is meant to be located.
Additionally, project teams should give special consideration to thermal performance and the potential for water penetration when designing the junctions between modules. If not detailed appropriately, the connection plates installed at exterior mate lines can result in thermal bridging. The careful design of connections is also crucial to fire resistance, as it’s important to maintain fire resistance at all joints— both between modules and between the modules and the façade system.
From an aesthetic standpoint, designers should address how mate lines on the interior and exterior will be treated to either express the modular construction methodology or conceal it.
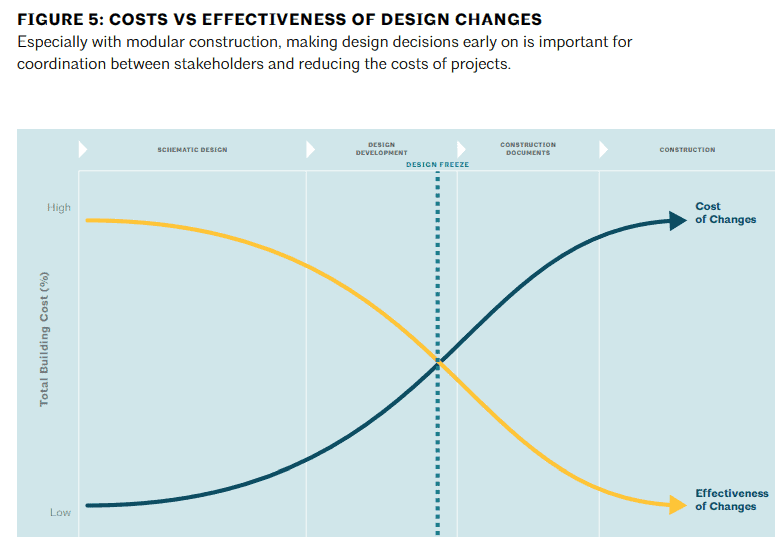
Design for disassembly
Modular projects may be designed to enable disassembly—whether it’s to maximize sustainability or to meet a project requirement for future relocatability or repurposing. This generally entails a higher degree of simplicity and repetition at the component level as well as access to connections. In modular construction, design for disassembly also involves maximizing the proportion of components manufactured off-site. A building completed 90 percent off-site will generally consist of more distinctly modular components and be more easily disassembled than a building completed 50 percent off-site and 50 percent on site, which will likely consist of fewer modular components and thus require more demolition. (For information on this approach, see the AIA Practice Guide on Design for Adaptability, Deconstruction, and Reuse.)
For disassembly design features to be effective, of course, they must be apparent to and understood by whatever parties in the future may be responsible for the building’s deconstruction. The design team should produce documentation of how the building was put together and how it’s meant to be taken apart.
Modularization
Once the building design has been fully developed, the modular manufacturer will work with the design team to create a “modular key plan”—essentially a plan for how the building will be divided into constitutive modules.
Ideally, the modular key plan will maximize the size of modules in order to minimize the total amount to be fabricated, transported, and installed. The maximum dimensions of the modules will depend on applicable transportation regulations, which may vary region to region. Modules typically measure between 12- to 14-feet wide, 50- to 60-feet long, and 11.5- to 13-feet high.
When dividing the building into modules, it’s essential to make sure there are no conflicts at mate lines. It may be necessary, in some cases, to make slight adjustments to floor plans if elements conflict, giving preference to the modularization for purposes of efficiency.
In general, the modular manufacturer’s in-house structural engineers will be responsible for designing “pick points”—for crane lifting and placing—to be included in the fabrication of each module. And once the modular key plan is finalized, with the structure’s bearing points and loads established, it will be used to design the foundation.
Design freeze
It’s important to establish a design freeze when using a modular construction approach because design changes late in the process can be costly. Unlike traditional construction processes— which are more sequential and make it relatively easy to make design changes—a lot of the work is done simultaneously in modular construction processes, leaving little time in the schedule for alterations.
Post Design (Construction Phase)
When the design has been finalized, materials should be ordered according to the production schedule. Project teams should coordinate with the modular manufacturer to make sure that products and materials with longer lead times are ordered in advance to avoid possible delays.
Manufacture and site preparation
As discussed, a primary benefit of modular construction is that it allows for building components to be constructed at the same time that site work is being completed. Once manufacture and site operations commence, the project manager should maintain regular communication with the modular manufacturer and the construction manager to make sure that the parallel processes are closely coordinated and proceeding in step with each other, according to the schedule.
Transport, staging, assembly
Ideally, in order to maximize the benefits of modular construction, a just-in-time (JIT) delivery schedule should be implemented to reduce the need to store completed modules on-site. However, in many cases, because of the sometimes-unavoidable imprecision of transportation due to such factors as permitting and traffic, a JIT delivery schedule may not be feasible. In such situations a staging area able to accommodate a predetermined number of modules will be required, allowing for continuous offloading.
Delivery timetables should be carefully coordinated and adjusted according to the progress of the assembly process. Depending on the size of the project, the fabrication process may need to be expedited or scaled up to keep pace with the rapid speed at which the modules can be assembled. This may not be a concern for small projects, but on larger mid-rise and high-rise projects—especially those in dense urban areas with limited space for storage on-site—it is critical that the production, transport, and assembly of modules is balanced so that there’s neither time wasted waiting for modules from the manufacturing facility nor a backup of modules on-site waiting to be installed.
Because transportation regulations vary according to location and are handled state-by-state, if modules are manufactured in a different state than the project site, there will be a series of differing codes to comply with. In addition, the particular constraints of the project site, including the amount of space available for staging, will also affect the rate at which modules are shipped. If sufficient space is available, multiple modules may be staged simultaneously; if there is limited space, modules may need to be lifted and installed directly from the truck.
Once the modules are placed, they are connected together and then fastened to the foundation. The envelope is then secured by installing infill sheathing at all mate lines and, depending on the level of finish completed off-site, secondary water and air barriers and exterior cladding where necessary. This can be critical to the thermal energy performance of the building, especially in cold-weather climates.
An Evolution of Practice
Organizations such as Modular Building Institute predict there will be a significant shift towards modular and other off-site construction approaches in the coming years—if for no other reason than the shortage of labor continue to be exacerbated as large numbers of skilled construction workers retire and are not replaced. In addition, as most other major industries have evolved to rely on more industrial and automated processes, it’s seen as inevitable that the building industry will do the same, for example, by shifting more and more to approaches like modular construction. The fact that some large general contractors have recently started modular construction divisions while others have partnered with existing modular manufacturers shows that this transformation has begun.
In the meantime, new tools and strategies are regularly emerging, fostering an ongoing evolution in the way we design and construct buildings. Technologies such as robotics, sensors, cloud computing, and virtual reality are enabling project teams to pursue ever more ambitious and complex goals. But while building projects become more complex, requiring an increased level of specialty in the industry, the silos that have traditionally existed in the design and construction fields are being replaced by more integrated and interdisciplinary modes of operating. As design/build and IPD models become more common, encouraging more innovation, it may lead to evolved forms of practice, such as, for example a “master builder”–like model defined by construction process-led design.
Further reading: https://www.modular.org/
Thanks for the blog loaded with so much information. It’s really informative.
AAC Blocks Advantages
I’m impressed by the speed of construction with modular methods. It’s not just about saving time but also reducing the environmental impact. Great strides in sustainable building!